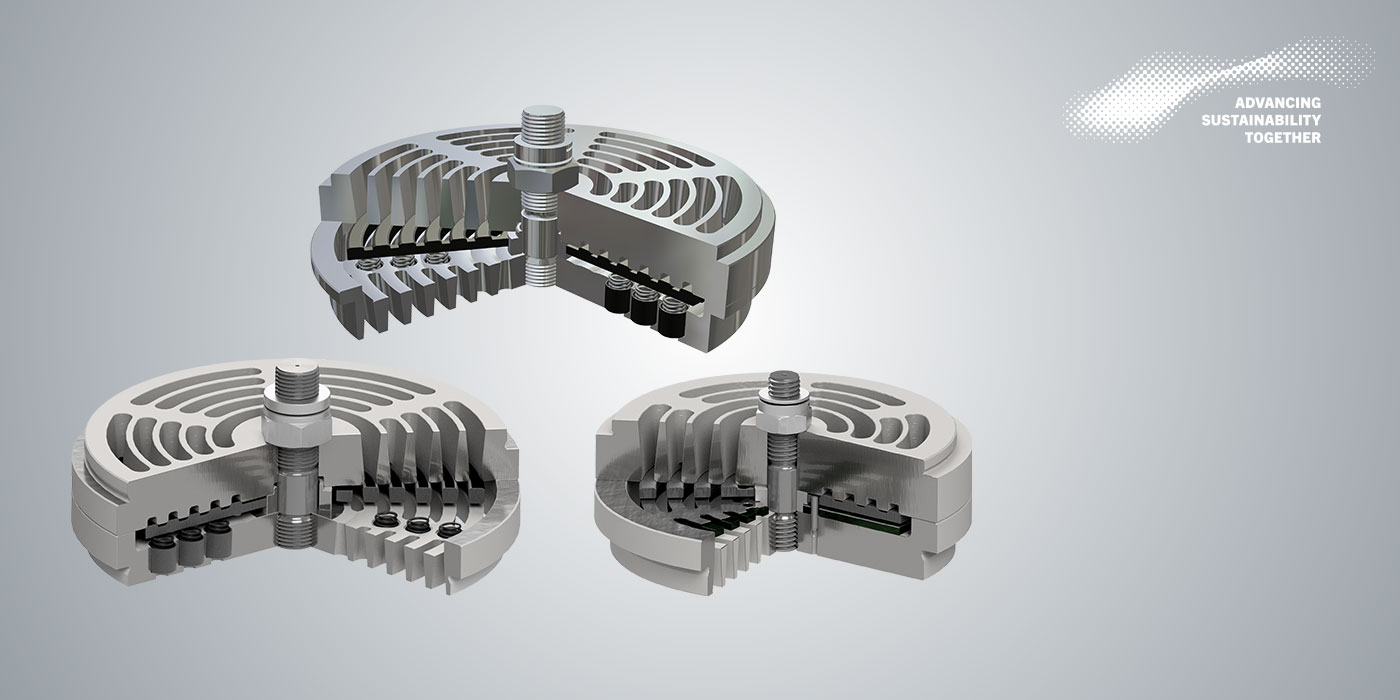
XP, CP, CPs – Profiled Plate Valves
For your process or natural gas application
The best valves in efficiency without sacrificing reliability
Conventional valve design has had its day when it comes to increasing the efficiency and uptime of compressors. Real increases in compressor efficiency can only be achieved through innovative designs. The compressor valve is the heart of the compressor, and significantly determines the overall compressor efficiency and uptime. To optimize reliability and saving energies, you need a technologically advanced valve that can do both. HOERBIGER’s XP and CP Profiled Plate Valve series combine all the properties to meet these requirements: PowerPEEK® plates with extreme efficiency and excellent flow characteristics for high compressor uptime. Further, you can drastically decrease the electric power and fuel consumption and reduce the related CO2 emissions when increasing the service life and up to 50% the efficiency in parallel. But not only that: thanks to the high degree of standardization, the number of different spare parts in the warehouse is reduced and inventory is made easy.
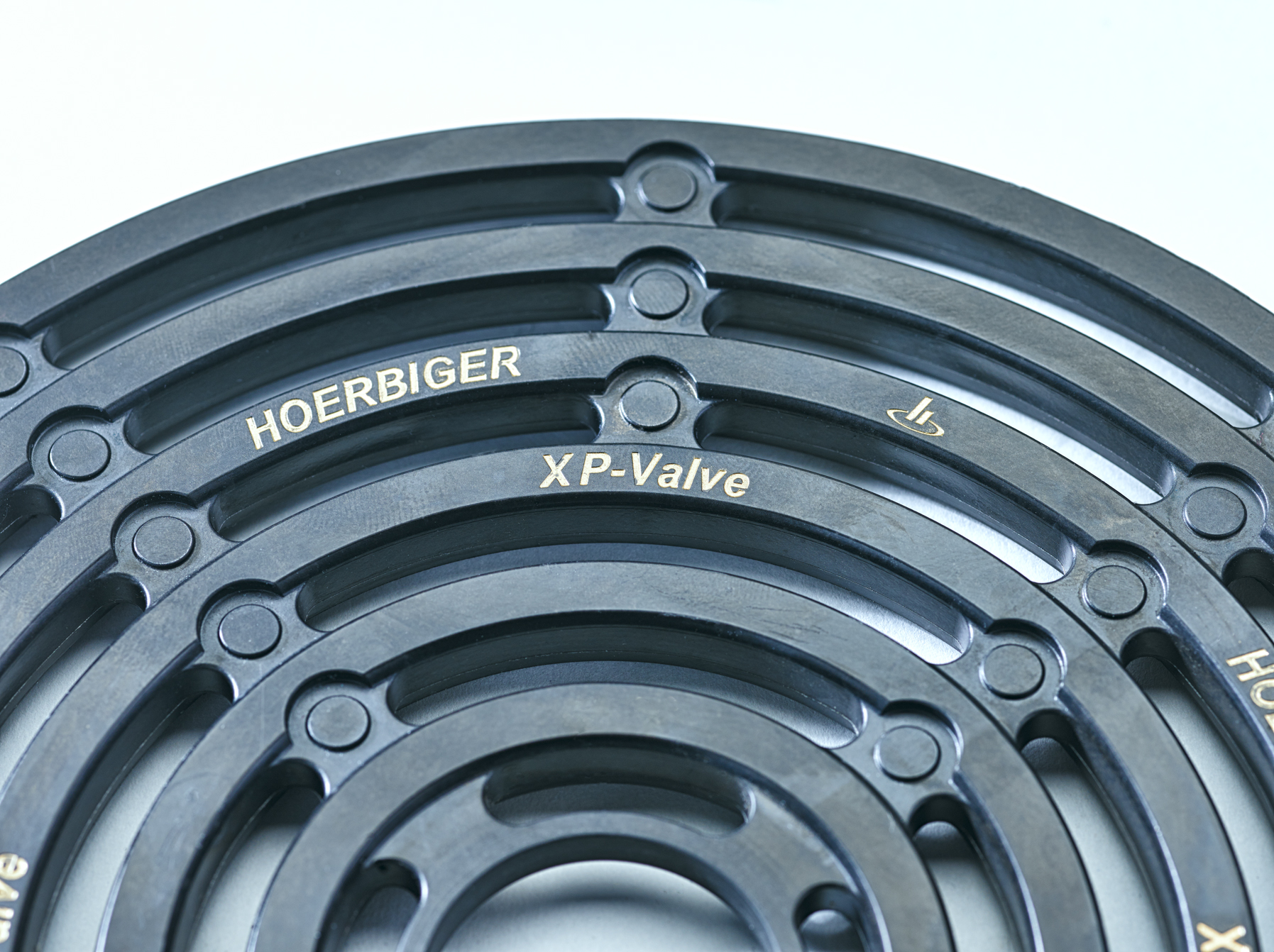
High efficiency and long life
PowerPEEK® and the unique design of profiled valve plates create a valve with extreme efficiency and excellent flow characteristics. This automatically improves the valve's reliability and durability. The construction of a finer-meshed ring section increases the effective flow area and hence the efficiency of the valve. The aerodynamic design generates a lower pressure drop than conventional valve sealing elements and gives small amounts of liquid and debris the ability to pass through. PowerPEEK® plates also offer an optimized orientation of reinforcing fibers for extreme strength and robustness. This leads to an increase in MTBF and MTBM and higher production output.
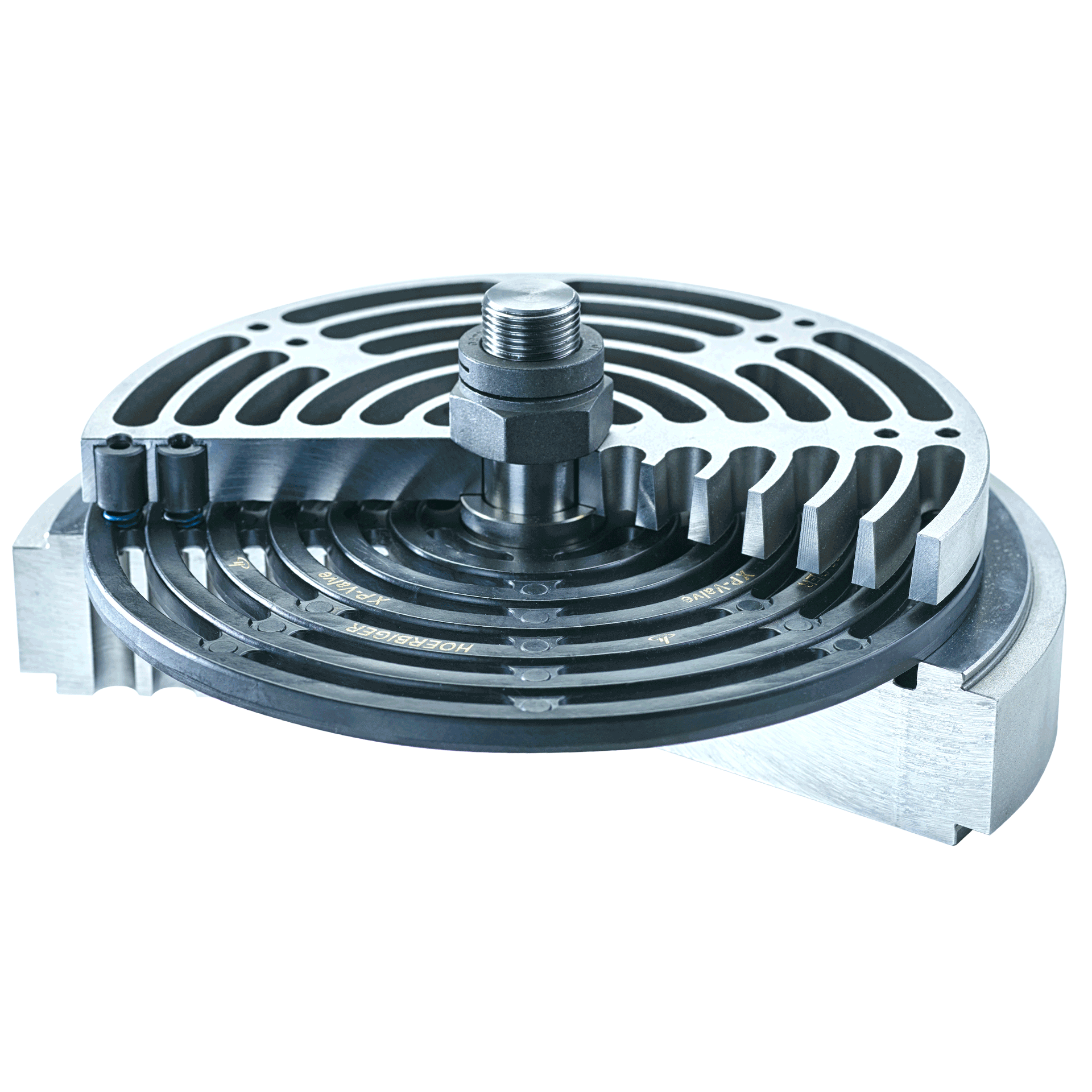
With XP Profiled Plate Valves, you are always a step ahead. Efficiency, energy savings, reliability and service life are all requirements for gaining an edge in the market, and our XP valves are the ideal component to deliver these improvements for reciprocating in process gas industries.
Benefits at a glance
- Profiled plate design and higher number of flow channels
- Spring savers prevent coil to guard contact
- Injection molded high-performance PEEK®
- Industry benchmark in efficiency: 30 - 50% higher effective flow area than conventional valves. Superior efficiency even at low lift
- Tribological optimization
- Optimum fibre orientation and high flexural strength. 4-6 time higher impact resistance than standard PEEK.
- Aerodynamic flow path
- Anti-stiction design: Waveshape profiled guard and tapered seat
- Heavy duty springs made of ESR steel (Electro slag remelting)
- Reduces build up of particles and provides tolerance of liquids
- Reduces adhesion forces due to liquids. Avoids delays in valve opening and closing. Tolerance against over-lubrication or liquid carry over.
- Designed for high dynamic loads
- Industry benchmark in efficiency
- High performance valve plate
- Tribological optimization
- Replace wear parts less frequently (longer service intervals)
- Reduce main driver energy costs
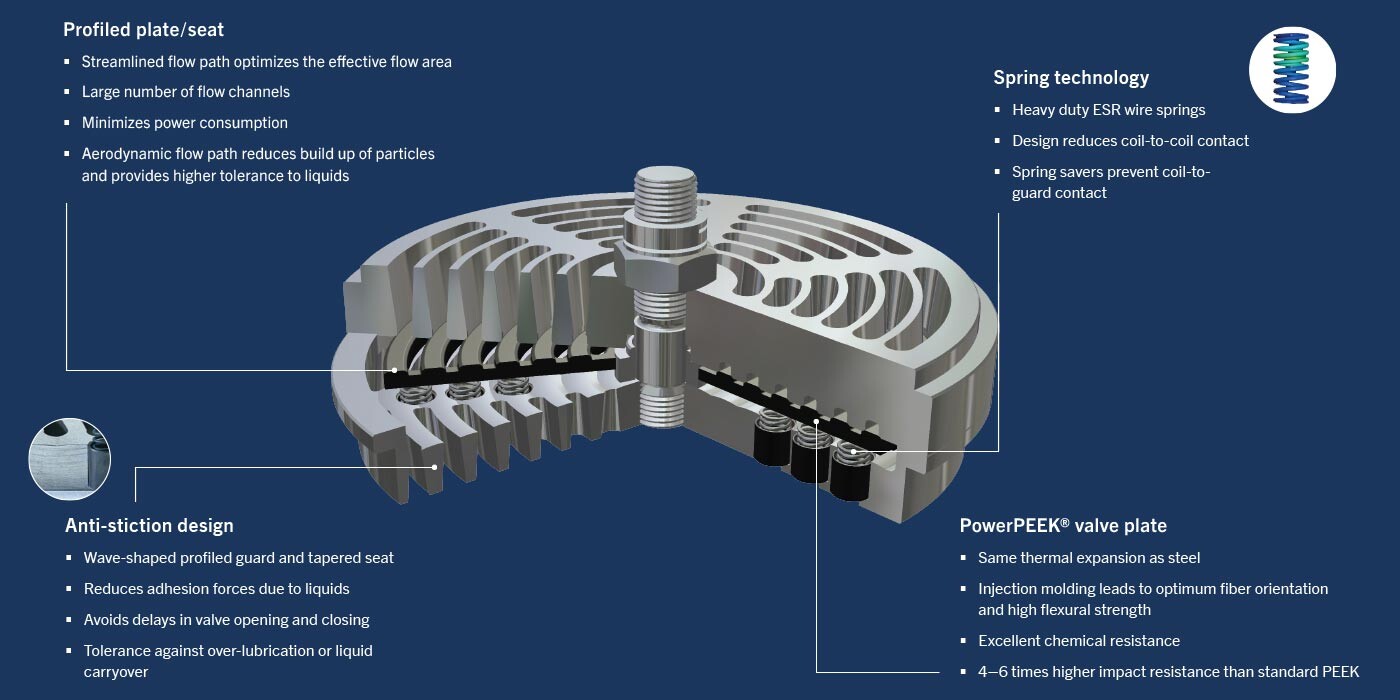
- Main application:
- Process gas
- Max. discharge pressure:
- 300 bar
- Max. differential pressure:
- 200 bar*
- Min. suction temp.:
- -40°C
- Max. discharge temp.:
- 230°C
- Mol weight:
- 2-50 g/mol
- Max. speed:
- 1,500 rpm
- Cylinder lubrication:
- lube/ non-lube
- Type diameter:
- 86-262 mm
- * Maximum allowable differential pressure
- depending on gas temperature.
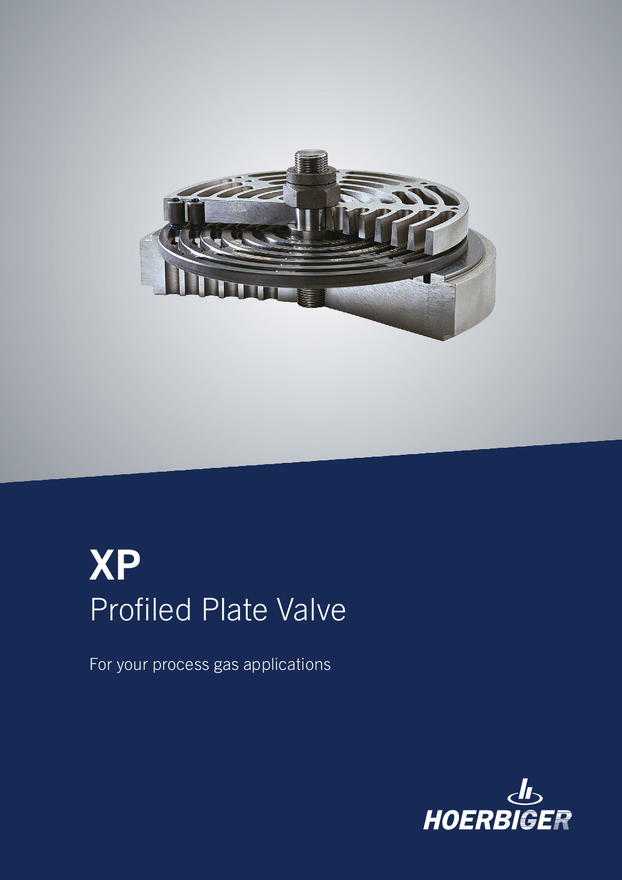
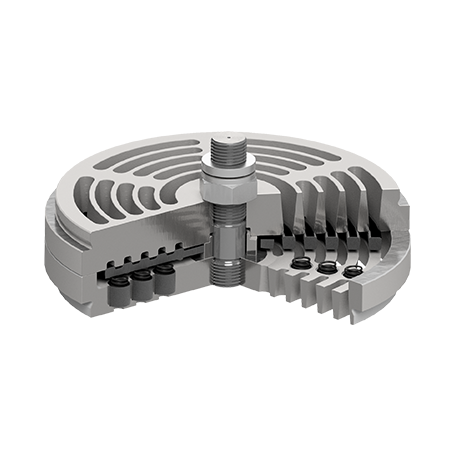
CP Profiled Plate Valves technology offers maximum efficiency, despite minimal lift, and excellent closing properties. Additionally, HOERBIGER created PowerPEEK® an innovative material that ensures robustness and durability – resulting in longer service life for valves and avoiding unplanned compressor downtime. These are properties that are important for compressors in natural gas applications.
Benefits at a glance
- Profiled plate design and higher number of flow channels
- Spring savers prevent coil to guard contact
- Injection molded high-performance PEEK®
- Industry benchmark in efficiency: 30 - 50% higher effective flow area than conventional valves. Superior efficiency even at low lift
- Tribological optimization
- Optimum fibre orientation and high flexural strength. 4-6 time higher impact resistance than standard PEEK.
High effective flow area
Lower power/flow ratio making more horse power available for increased flow
- Aerodynamic flow path
- Anti-stiction design: Waveshape profiled guard and tapered seat
- Heavy duty springs made of ESR steel (Electro slag remelting)
- Reduces build up of particles and provides tolerance of liquids
- Reduces adhesion forces due to liquids. Avoids delays in valve opening and closing. Tolerance against over-lubrication or liquid carry over.
- Designed for high dynamic loads
- Industry benchmark in efficiency
- High performance valve plate
- Tribological optimization
- Replace wear parts less frequently (longer service intervals)
- Reduce main driver energy costs
- High standardization
- Reduced valve configurations
Commonality of parts
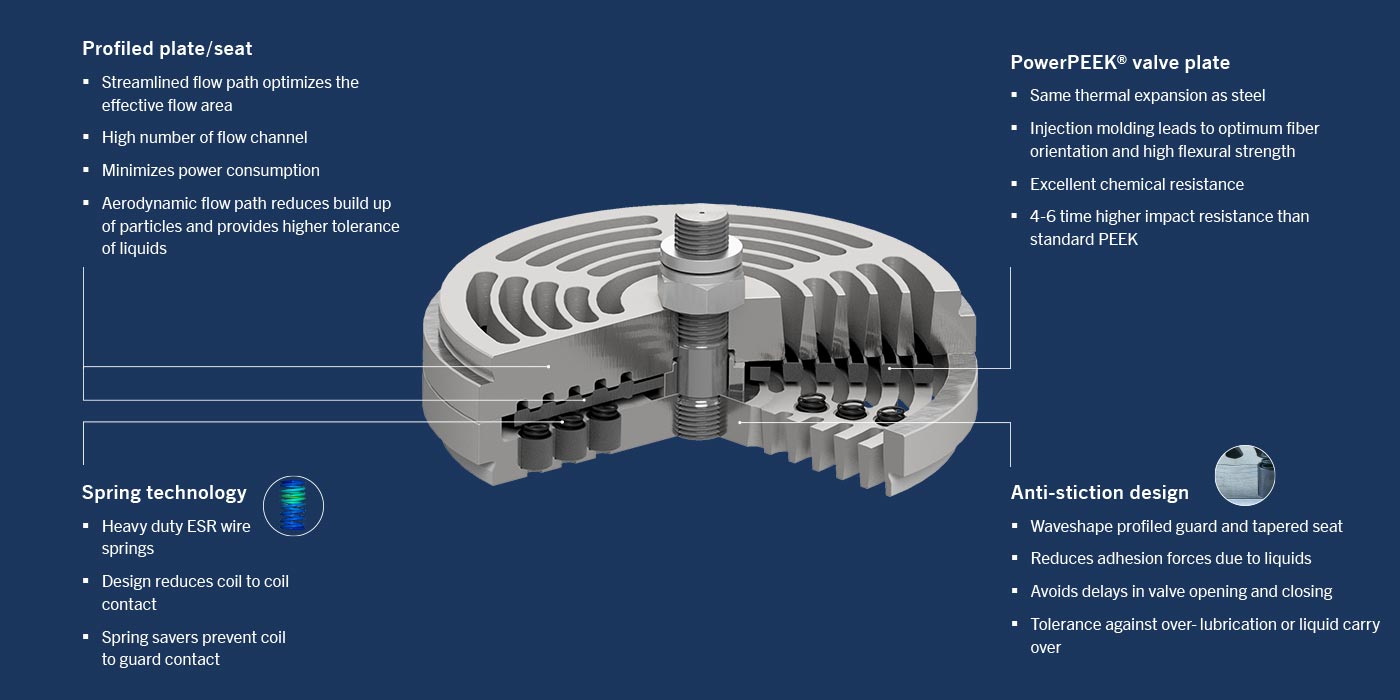
- Main application:
- Natural gas
- Max. discharge pressure:
- 300 bar
- Max. differential pressure:
- 200 bar*
- Min. suction temp.:
- -40°C
- Max. discharge temp.:
- 230°C
- Mol weight:
- 12-80 g/mol
- Max. speed:
- 1,800 rpm
- Cylinder lubrication:
- lube/ non-lube
- Type diameter:
- 88-212 mm
- * Maximum allowable differential pressure
- depending on gas temperature.
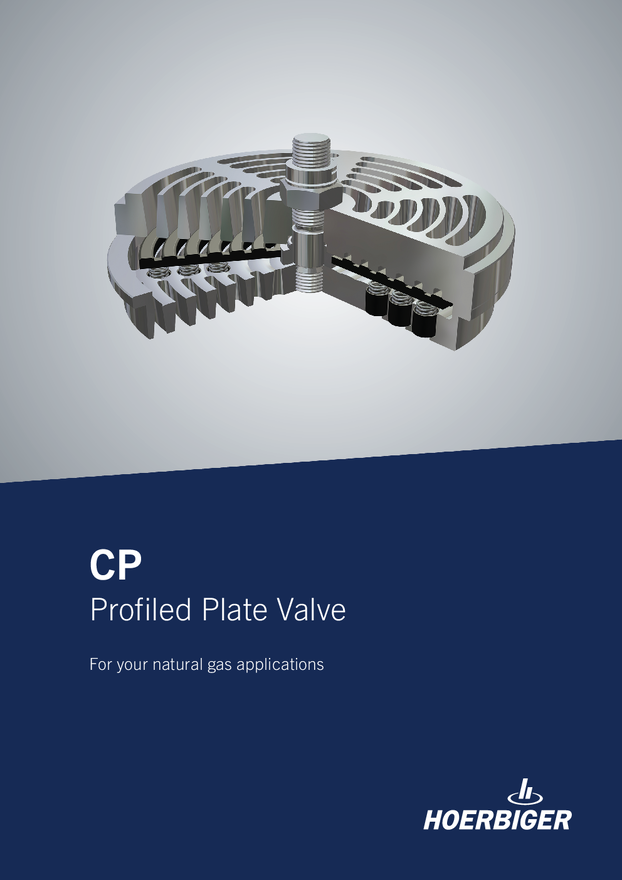
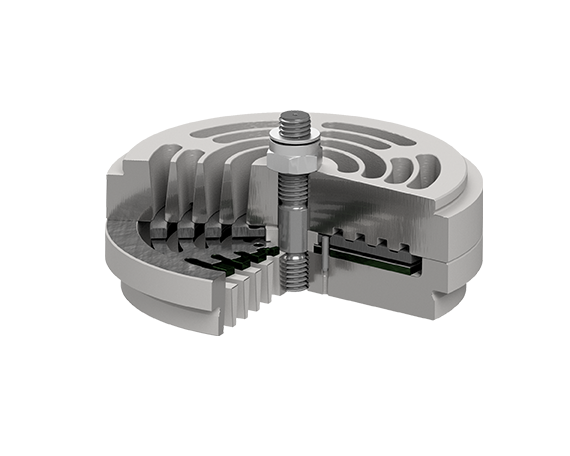
CPs Profiled Plate Valves technology offers maximum efficiency, despite minimal lift, and excellent closing properties. The CPs valves offer up to 50% higher effective flow area than conventional valves and make horsepower available for increased throughput. The high performance PowerPEEK® valve plates outperform any other PEEK valve plates in terms for impact resistance and strength.
But not only that: thanks to the high degree of standardization, the number of different spare parts in the warehouse is reduced and inventory is made easy.
The valves are also the ideal choice for biogas / green methane compression.
Benefits at a glance
- Profiled plate design and higher number of flow channels
- Damping plate
- Injection molded high-performance PEEK®
- Industry benchmark in efficiency: 30 - 50% higher effective flow area than conventional valves. Superior efficiency even at low lift
- Cushions opening impacts of valve and spring plates. Accommodates tips of spring plate when valve is open
- Optimum fibre orientation and high flexural strength. 4-6 time higher impact resistance than standard PEEK.
High effective flow area
Lower power/flow ratio making more horse power available for increased flow
- Aerodynamic flow path
- Anti-stiction design: Waveshape profiled guard and tapered seat
- Heavy duty spring plate
- Reduces build up of particles and provides tolerance of liquids
- Designed for high dynamic loads in high-speed compressors
- Reduces adhesion forces due to liquids. Avoids delays in valve opening and closing. Tolerance against over-lubrication or liquid carry over.
- Industry benchmark in efficiency
- High performance valve plate
- Heavy duty spring plate
- Replace wear parts less frequently (longer service intervals)
- Reduce main driver energy costs
- High standardization
- Reduced valve configurations
Commonality of parts
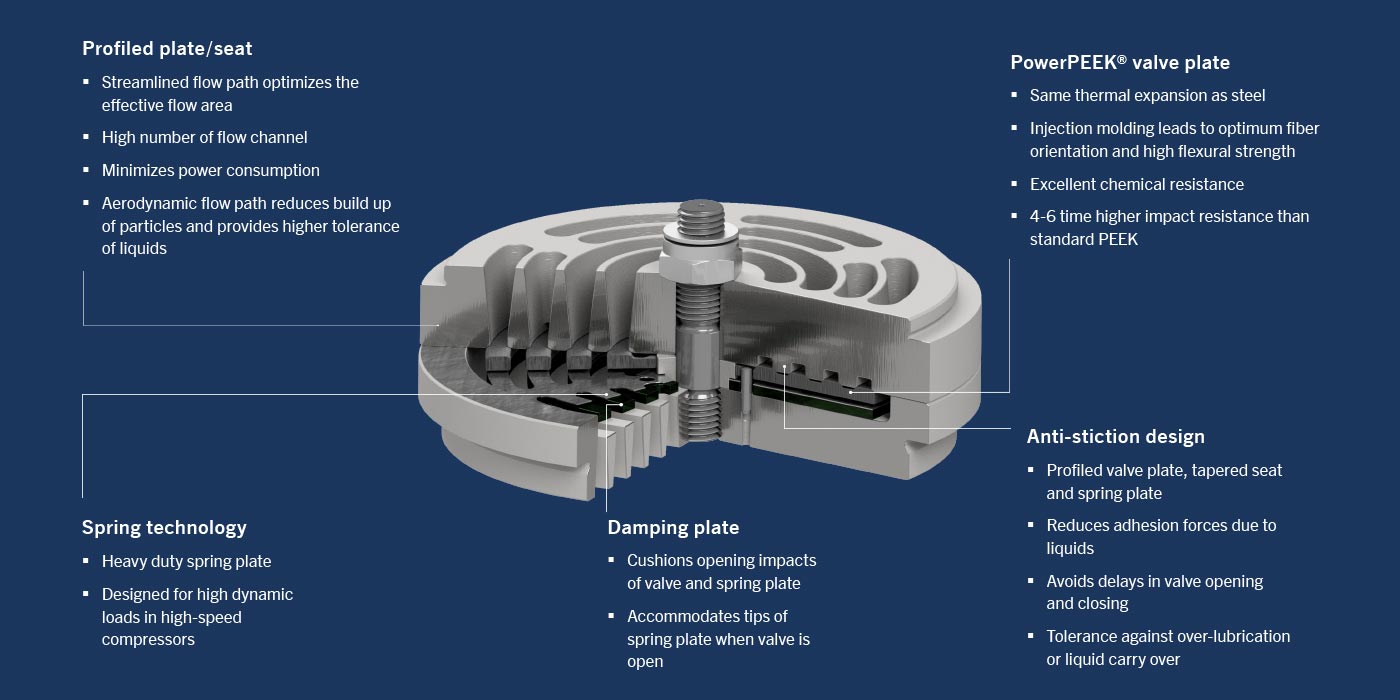
- Main application:
- Process gas
- Max. discharge pressure:
- 300 bar
- Max. differential pressure:
- 200 bar*
- Min. suction temp.:
- -40°C
- Max. discharge temp.:
- 230°C
- Mol weight:
- 12-80 g/mol
- Max. speed:
- 2,800 rpm
- Cylinder lubrication:
- lube/ non-lube
- Type diameter:
- 38-90 mm
- * Maximum allowable differential pressure
- depending on gas temperature.
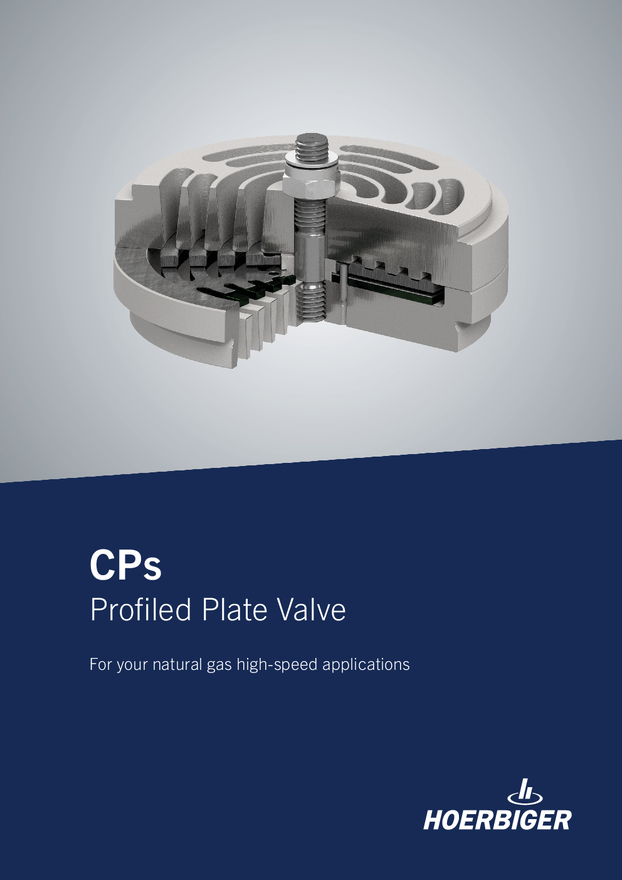
How can we help you?
Let us know if you need assistance or have questions – one of our compression representatives will contact you as soon as possible.
Don’t miss out on the latest news!
Sign up below to receive the latest news and updates from HOERBIGER about our compression products and services.